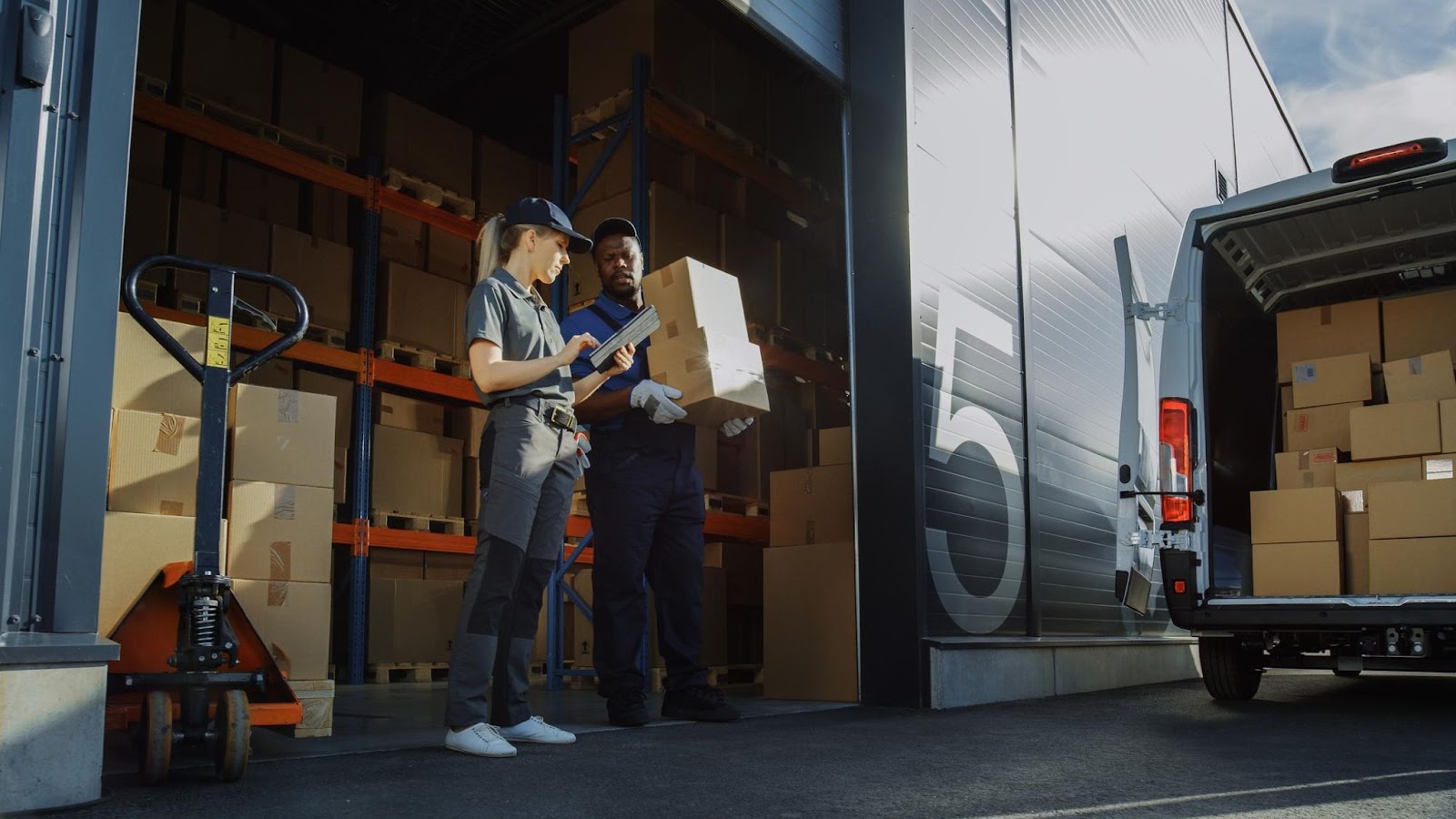
Route Optimisation is complex and often challenging to explain to non-technical stakeholders. Breaking it down into four steps clarifies what it does and how it benefits Logistics Providers.
How Logistics Providers operate
A 3PL (third-party logistics provider) offers outsourced logistics services, including warehouse management, order processing, and transportation. FMPs and LMPs (first- and last-mile providers) specialise in pickup and delivery stages. 3PLs often organise local transportation while FMPs and LMPs execute it.
These "Logistics Providers", or LPs, for simplicity, use Route Optimisation systems to find the best set of routes for multiple stops in their transportation process. Algorithms consider all stops, time windows, vehicle capacity, driver schedules, traffic, and other constraints. "Best" can mean fastest, shortest, cheapest, most productive, or lowest in fuel costs or vehicle wear. Optimisation focuses on the set of routes for a given operational 'unit' – e.g., a service area, order batch, or service type.
Why Route Optimisation?
For LPs, the primary benefits of Route Optimisation are efficiency gains and cost savings, as well as the improvement of service offerings and customer experience. In international transportation, first—and last-mile operations account for 35-45% of total operating costs. In domestic transportation, it is 60-75%. The most compelling argument for starting a Route Optimisation initiative is that more stops for less time, mileage, and fuel per route reduce the cost per stop and consignment.
It makes sense: even in a mature logistics operation, Route Optimization can yield efficiency gains of upwards of 20%.
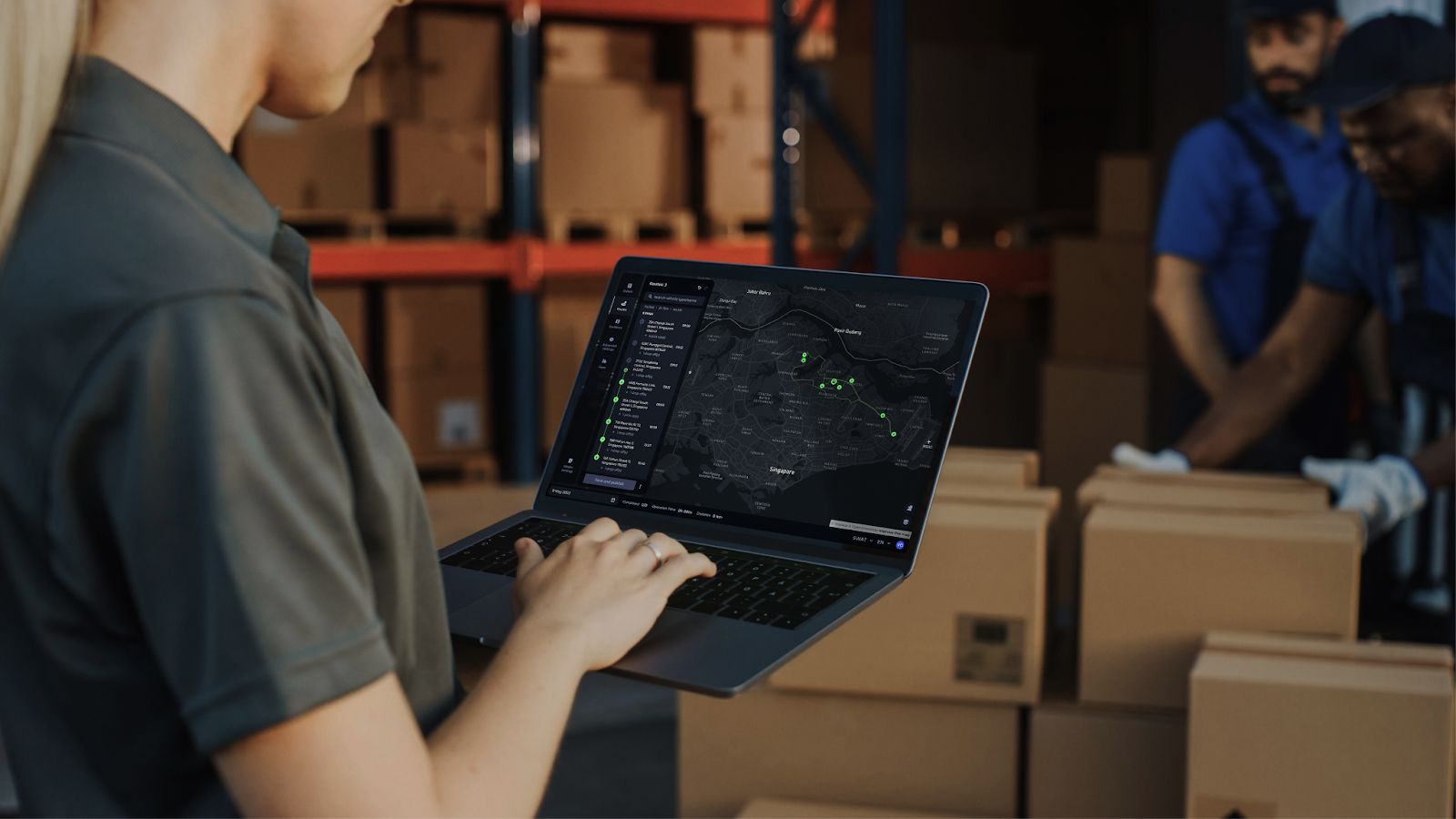
So, is Route Optimisation a no-brainer?
Despite these apparent benefits, companies often struggle to prove them and free up the funds and resources needed to deploy a Route Optimiser. I speak from my own experience and that of other Ops Tech veterans in the industry, having spent countless hours estimating Route Optimisation project P&Ls.
The primary reason is the lack of understanding of what a Route Optimiser does and where to seek the benefits. Intuitively, decision-makers tend to zoom in on stop sequencing as the vital benefit driver and, therefore, like to test Route Optimisers on individual routes (before vs. after). This often yields disappointing results, as human drivers (especially experienced ones having serviced the same area and customers for years) easily beat the algorithms on their own or with simple and free tools like Google Maps.
What does Route Optimisation do?
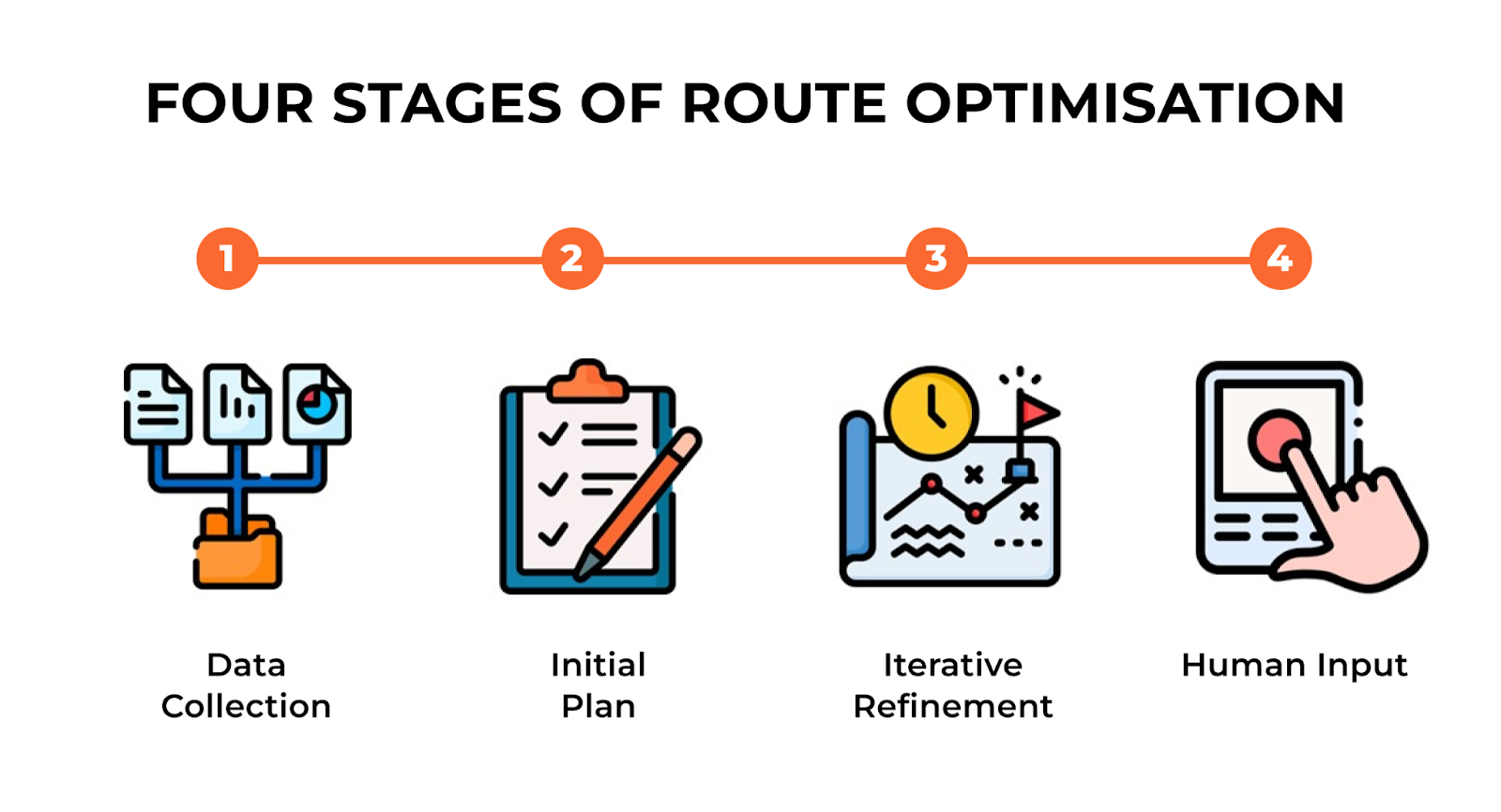
To demystify this, let’s break down what a (full-featured) Route Optimiser does into four fundamental steps:
- Gathering Information—A Route Optimiser starts by collecting all the necessary data. This includes delivery addresses, what needs to be picked up or delivered, when it needs to arrive, and any special instructions. Think of it as gathering all the puzzle pieces before assembling them.
- Creating an overall route plan - Next, the system plans an initial set of routes, considering millions of possible combinations to find the best way to perform all the stops. It also applies constraints, such as time windows, available vehicles, driver schedules, or road speeds. Depending on the type of services being provided and the expected fluctuations in workload, this plan might be created at varying intervals – quarterly, monthly, weekly, or daily.
- Refining the plan - Once the initial plan is in place, the optimiser starts fine-tuning it. Typically, this happens daily and sometimes multiple times a day. It fills up each route with appropriate stops, matches it with the right vehicle and driver, and puts the stops in the best order. But the system doesn't stop there. It keeps making minor adjustments to see if it can maximise efficiency.
- Human input - Finally, experienced dispatchers can review and adjust the routes based on their knowledge of the area and customers.
Even developers of Route Optimisers will tell you that step 3 is where the magic happens because it turns a good plan into a great one. But my question is this: Would you rather own the best house on the worst street in town or the worst house on the best street in the city?
How to make a successful case for Route Optimisation
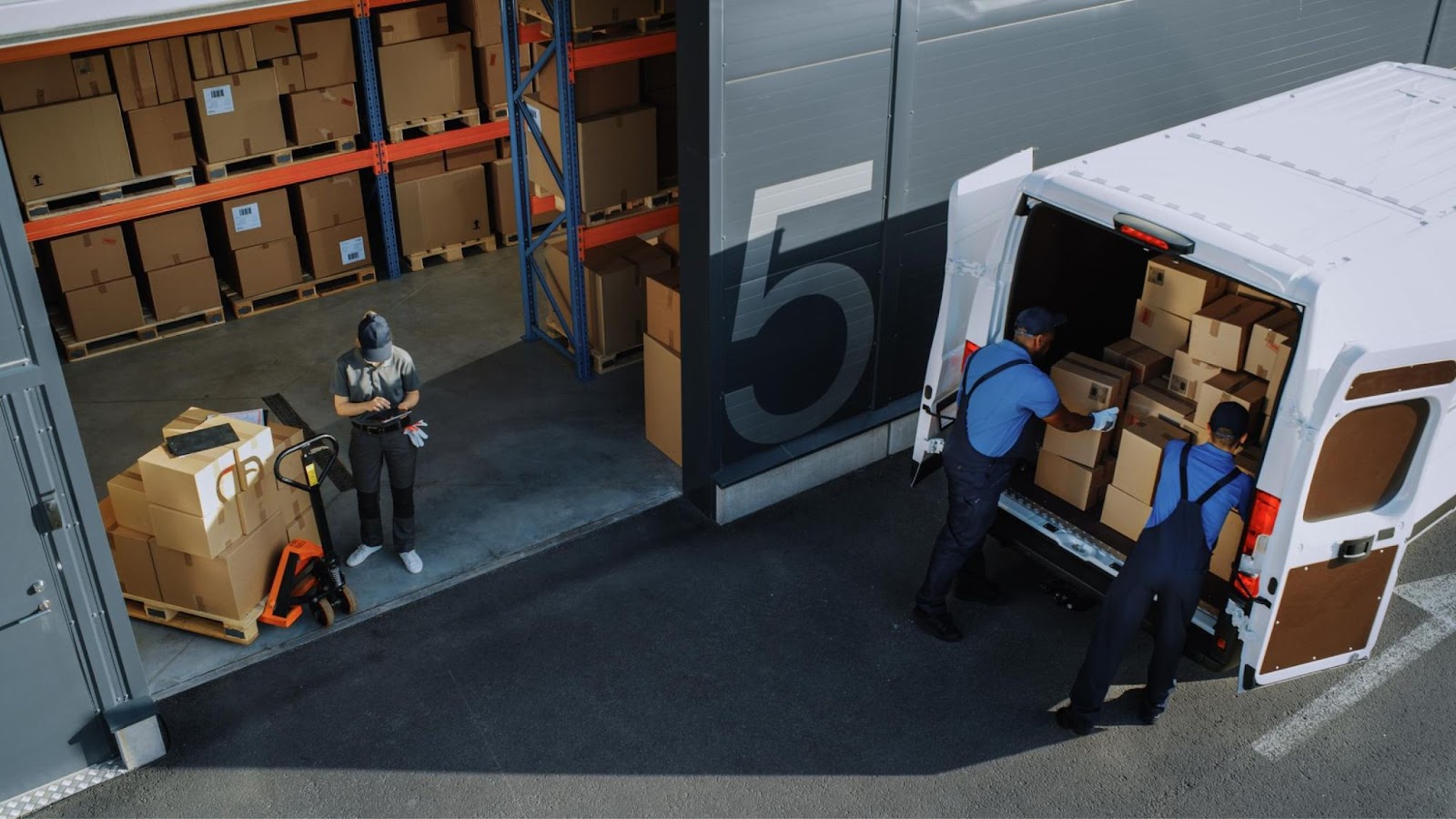
The overall route plan is critical! It sets the stage for how many resources are required and drives other business planning activities, with an impact beyond routes alone. Think of vehicle lease contracts, variable labour agreements (loaders, handlers, even drivers), or warehouse rentals that span months, if not years. These agreements often ask for a minimum committed spend and impose penalties for deviations. Getting those wrong can be very costly.
Of course, refining the plan is important, too, as it determines how the resources are used once they’ve been allocated. But without an efficient initial route plan, companies risk starting their day-to-day operations with a sub-optimal design—and even after refinement, the entire route structure will still not be fully efficient.
To make a case for Route Optimisation, companies shouldn’t stop at the daily gains from route sequencing or load optimisation but also quantify the impact on short- to long-term route planning.
While estimating evidence of route sequencing benefits may require real-world proof of concept projects, route planning benefits can be calculated through simulation with historical data.
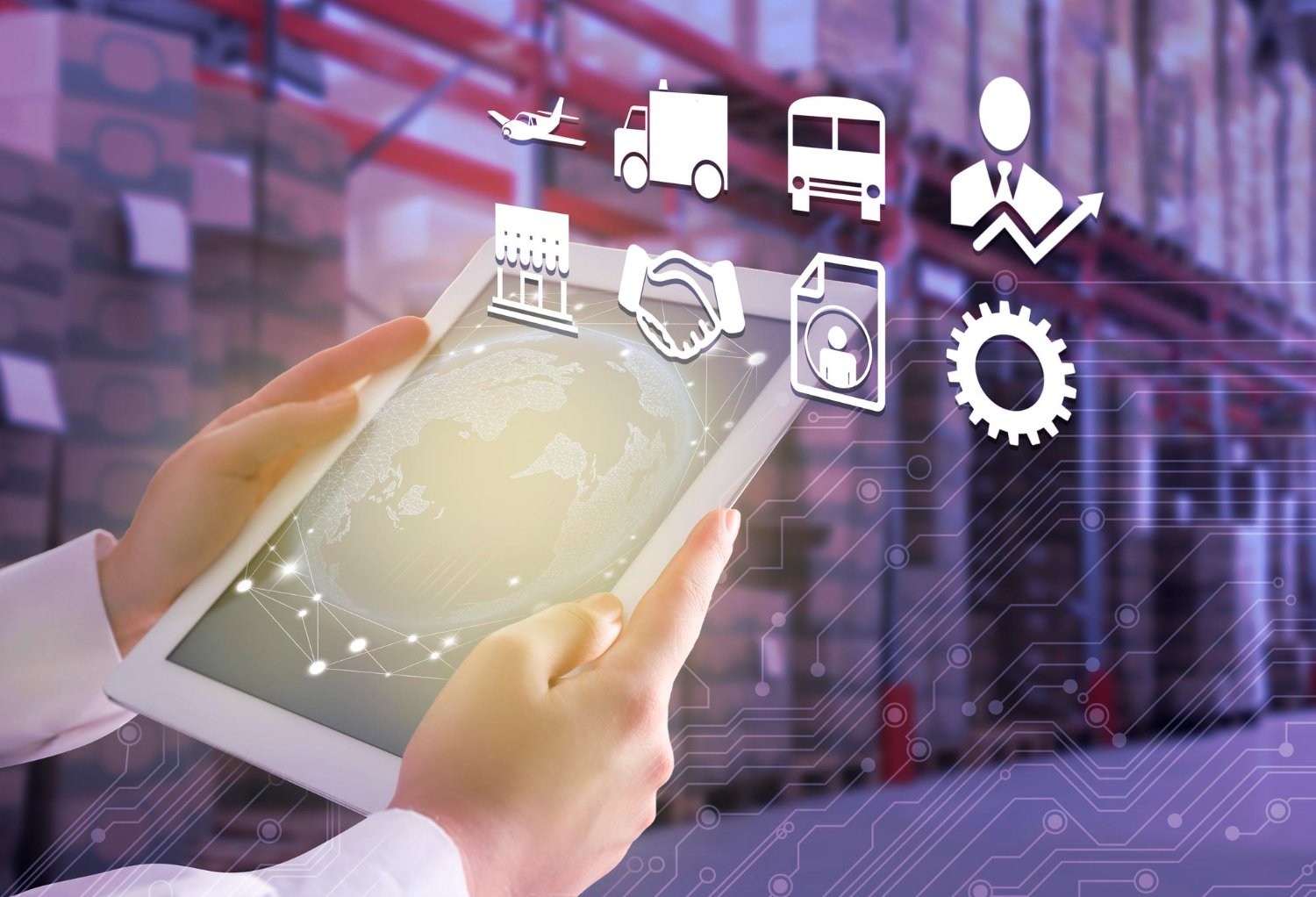
Fleet Management System Enhancing Dispatch Efficiency
A robust fleet management system enables businesses to monitor vehicle performance, driver behavior, and fuel usage in real-time. By leveraging data-driven insights, companies can make informed decisions that enhance operational efficiency and extend the lifespan of their fleet assets.
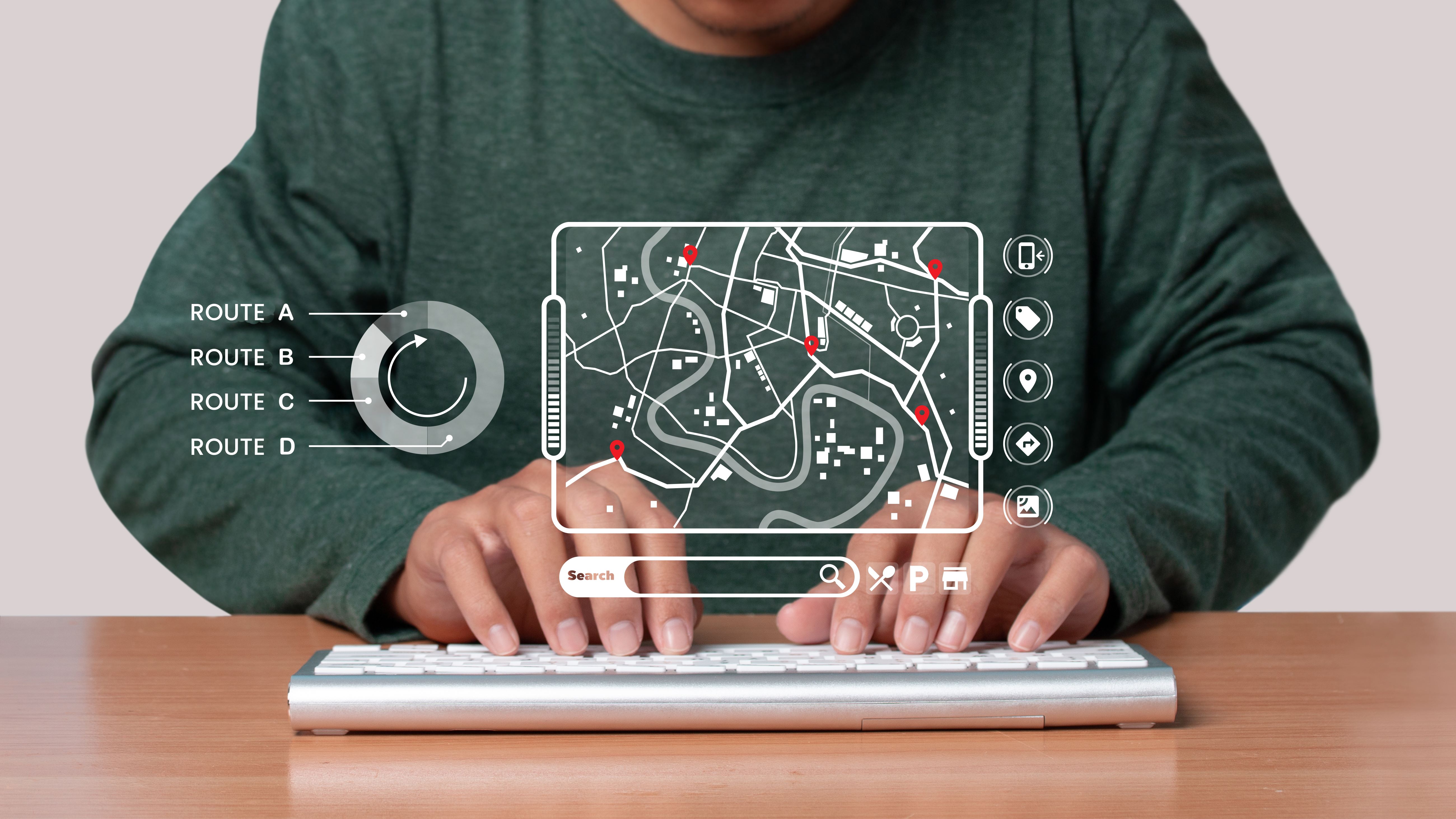
Achieving Seamless Omnichannel Logistics
Discover how omnichannel logistics is reshaping the future of retail by unifying inventory, fulfilment, and delivery across all channels. Learn how SWAT Mobility’s smart solutions empower seamless customer experiences and operational efficiency.
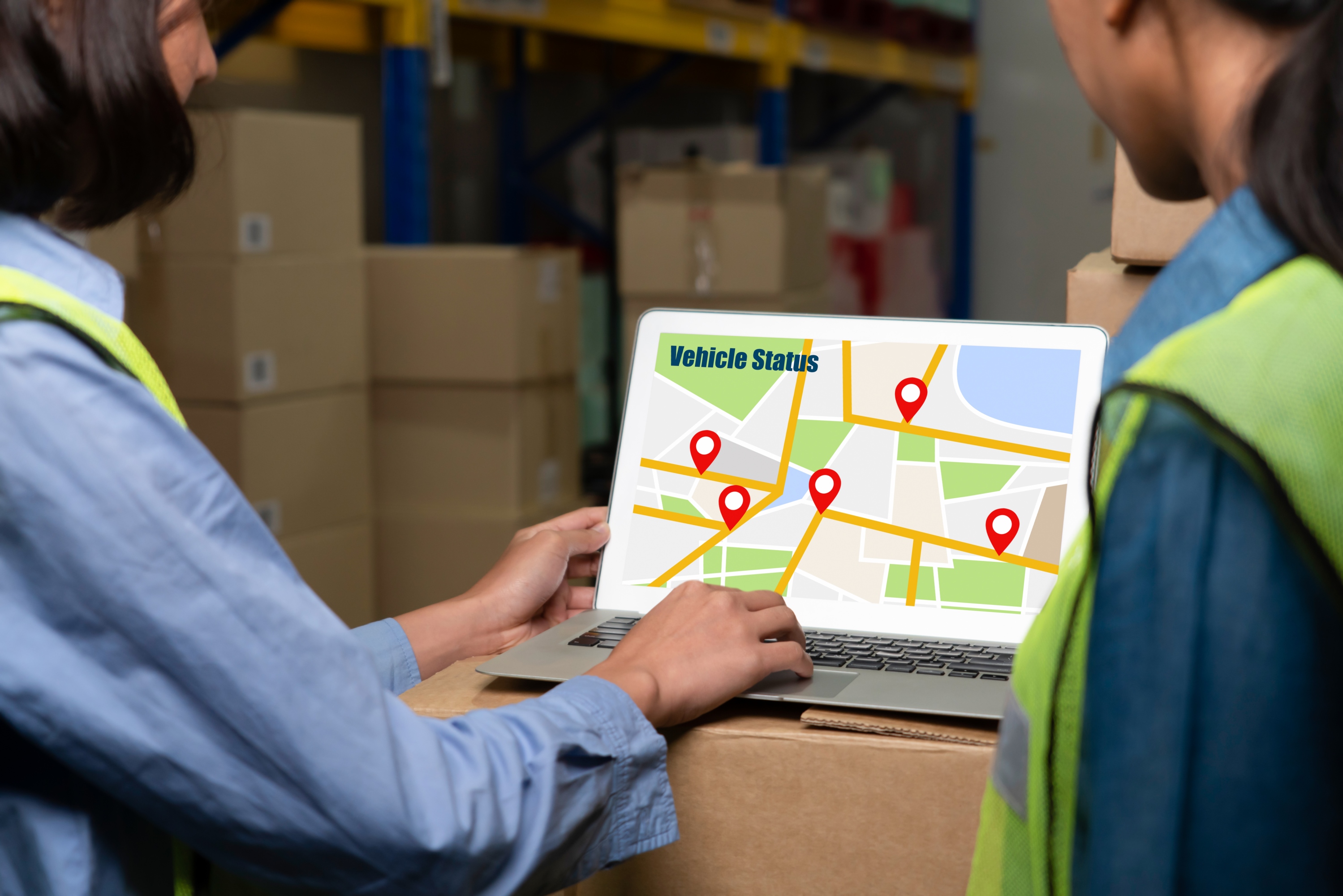
Sustainable Transport Management System
A transport management system (TMS) streamlines logistics by optimizing route planning, tracking, and fleet coordination in real-time. Discover how SWAT Mobility's TMS enhances operational efficiency and supports smarter, data-driven transport decisions.